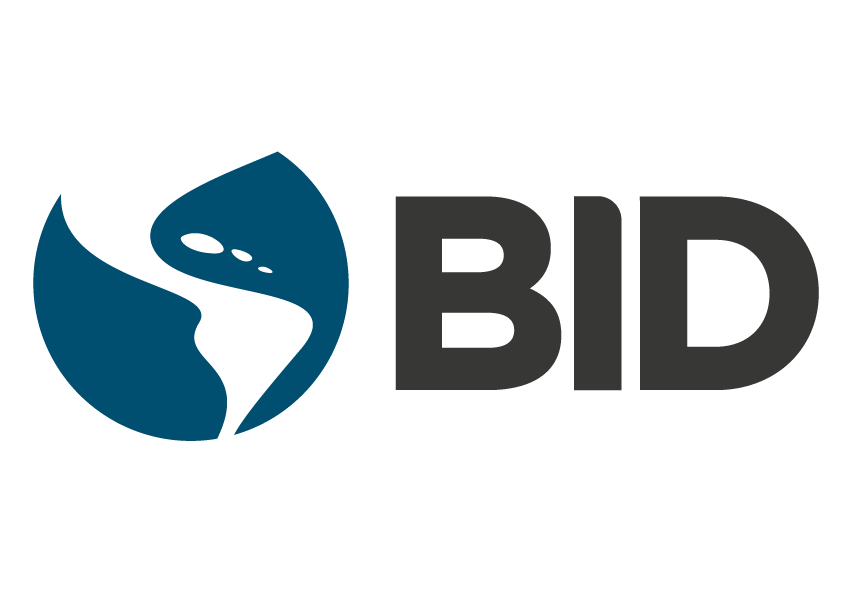
One of the most intriguing aspects of fluoropolymers is their inherent lubricity. Lubricity refers to the ability of a material to reduce friction and provide effective lubrication. For fluoropolymers, the lubricity of the material can be reflected by the coefficient of friction.
The coefficient of friction is a dimensionless value that represents the amount of friction between two surfaces in contact. It quantifies the ratio of the force of friction between two objects to the force pressing them together. It's important to note that the coefficient of friction is dependent on various factors such as the type of fluoropolymer, the roughness of the surfaces, the applied load, and the lubrication present.
Fluoropolymers owe their lubricity to their unique molecular structure, primarily composed of carbon-fluorine (C-F) bonds. These strong bonds create a non-stick surface with low surface energy, making fluoropolymers non-wetting and repelling other materials. As a consequence, when two surfaces come into contact, the low surface energy of fluoropolymers reduces the friction coefficient, leading to excellent lubrication properties.
Additionally, the strong C-F bonds contribute to the exceptional chemical and thermal stability of fluoropolymers, allowing them to maintain their lubricious nature even in extreme conditions. This outstanding stability, combined with low surface energy, makes them highly resistant to degradation or breakdown under harsh operating environments.
The coefficients of friction of common fluoropolymers vary depending on the specific grade and surface conditions. However, here are some typical values for reference. These values are approximate and may vary depending on factors such as surface finish, load, temperature, and lubrication.
Low friction fluoropolymer materials have a wide range of applications in various industries due to their unique properties. Some common application examples include: